Objectives
One of the work goals for TNO is to accomplish and establish mechanical properties of specimens that are printed by Orion.
Their second goal is that every specimen manufactured by Orion, has its quality visualized optically and also with a microscope.
FDM 3D Printing
Fused Deposition Modeling (FDM), or Fused Filament Fabrication (FFF), is an additive manufacturing process that belongs to the material extrusion family and is the most widely used 3D Printing technology. Typical FDM 3D printing, uses a plastic filament to print horizontal layers of plastic, typically to create very weak inter-layer bonding. This means the strength of the part is anisotropic (not isotropic/uniform) and that the tensile strength in the Z-direction (vertical orientation) is typically weaker.
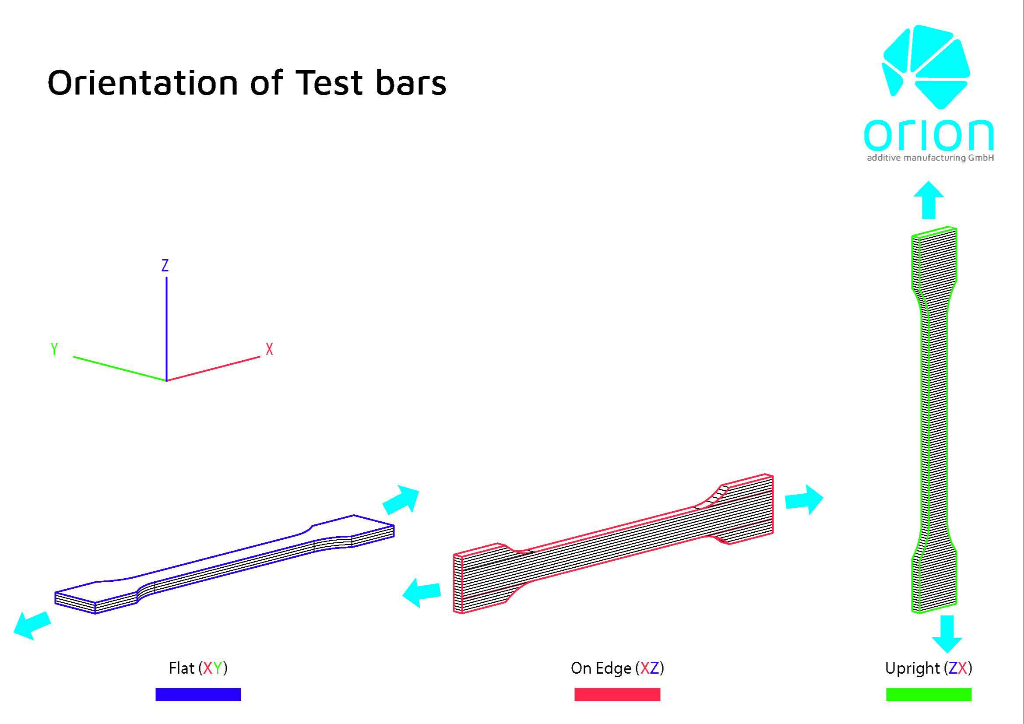
According to an article by 3D Hubs, "tensile test pieces printed horizontally in ABS at 50% infill were compared to test pieces printed vertically and were found to have almost 4 times greater tensile strength in the X and Y print direction compared to the Z direction (17.0 MPa compared to 4.4 Mpa) and elongated almost 10 times more before breaking (4.8% compared to 0.5%)."
FDM typically creates tensile strength in Z direction that is 1/4 of the strength in XY. But Orion AM's technology solves this by applying thermal radiation to heat the part, thus fusing the layers together and creating not only stronger parts but also watertightness.
Tensile Strength
36.3 MPa (XY) |
30.7 MPa (XZ) |
31.0 MPa (ZX) |
E-Modulus
2040 kPa (XY) |
1868 kPa (XZ) |
2096 kPa (ZX) |
Thermal Radiation Heating (TRH) Technology
Additive manufacturing through an FFF process typically produces weak inter-layer bonding, especially with High Performance Polymers like PEEK. This can result in anisotropic strength with a tensile stress in the Z-orientation as low as 10% of the material strength.
Orion AM’s proprietary technology efficiently heats the print from all directions up to 300 °C, thus increasing the inter-layer bonding and improving mechanical strength. This results in functional end-use parts including implants or aerospace parts.
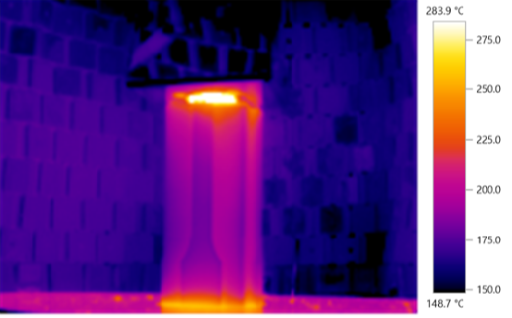
TRH Technology heating a PEEK 3D printed part up to 300 °C
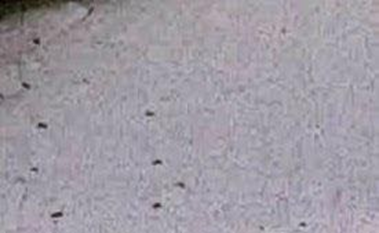
With Orion TRH
-Non-visible layers
-Homogeneous Structures
-Good inter-layer bonding
-High strength
-Suitable for end-use parts
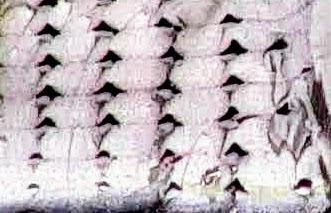
Without TRH
- Visible layers
-Porous Structures
-Weak inter-layer bonding
-Low Strength
-Suitable for prototypes only
Mechanical Results
ISO 527-1BA specimens measured with Instron Universal Testing Machine
Strain rate kept constant during measurement at 1 mm/
E- modulus determined with regression slope of 0,05% - 0,25% strain.
E-Modulus
Ultimate Tensile Strength
Conclusion
In conclusion, TNO found that as a whole the printed parts appear acceptable. The edges have some over extrusion that may result in stress concentrations during tensile testing. TNO also noticed no significant mechanical difference can be observed due to the layer heater when comparing the samples C170 & C185. Although a minor visual difference can be seen when comparing the two samples, corners seem less well-defined. For the most part in mechanical results, TNO observed that high modulus has been measured for E (box) samples, that is, statistically no different from the specimens. Lastly, TNO has observed fractures of tensile specimens show a breakage over several printed layers, that indicates good interlayer adhesion.


Support and Acknowledgements
This project was made possible through support of the AMable consortium and thank you so much to Phanindra Giddaluri at MonitorFish, Rob Kleijnen at Inspire AG, and lastly Guy Bex at TNO for their assistance. We appreciate everyone's cooperation.