A new approach to Additive Manufacturing
Overview
Fused Filament Fabrication (FFF) suffers from weak interlayer bonding, delamination, and warping because the material cools down after being deposited. This also leads to porous structures and lower relative part density resulting in weaker strength in 3D printed parts. Although some 3D printing systems use heated chambers to resolve this, they often use convection to heat the air which suffers from high heat losses and thermal gradients, thus limiting the heating of the material and thermal stability. Orion AM's process utilizes Thermal Radiation Heating which heats the material to much higher temperatures thus eliminating warping, distortion, and delamination.
Benefits
With Thermal Radiation the heat penetrates through the material, allowing the layers to truly fuse together. This results in parts that are more uniform in strength, more dense and stronger. This enables the full strength of the material and the production of end-use parts. The process is also capable of producing hermetically sealed parts, making it suitable for the production of seals, underwater housings and parts for vacuum applications.
Results
Orion's technology resolves the anisotropic nature of FFF 3D printing, even for difficult to print aerospace-grade materials like PEEK and PEI. This results in nearly isotropic properties.
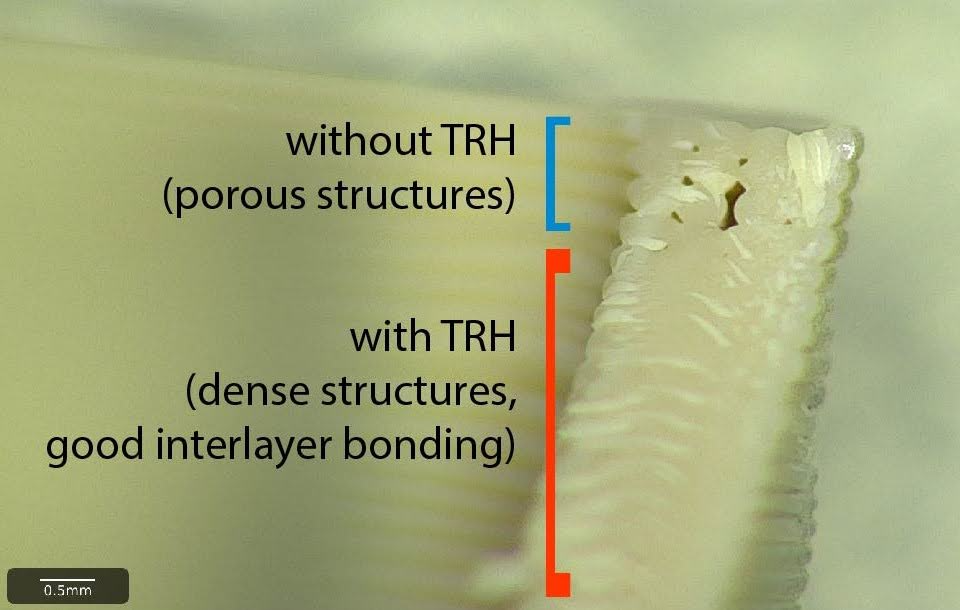
Fully Bonded Structures
When Thermal Radiation Heating (TRH) is not used, the print lines produce cold joints in between both the lines and the layers, resulting in weaker parts. This is depicted in the upper half of the print shown in the image.
In contrast, when TRH is activated, the internal structures are fully bonded, dense and without voids. This is shown on the bottom half of the print shown in the image
Solid Infill
A computerized tomography (CT) scan of Orion AM's specimens shows an average void content of less than 0.05%, meaning that the internal density of the structures are 99.95% dense, which is comparable to injection molding or CNC machining.
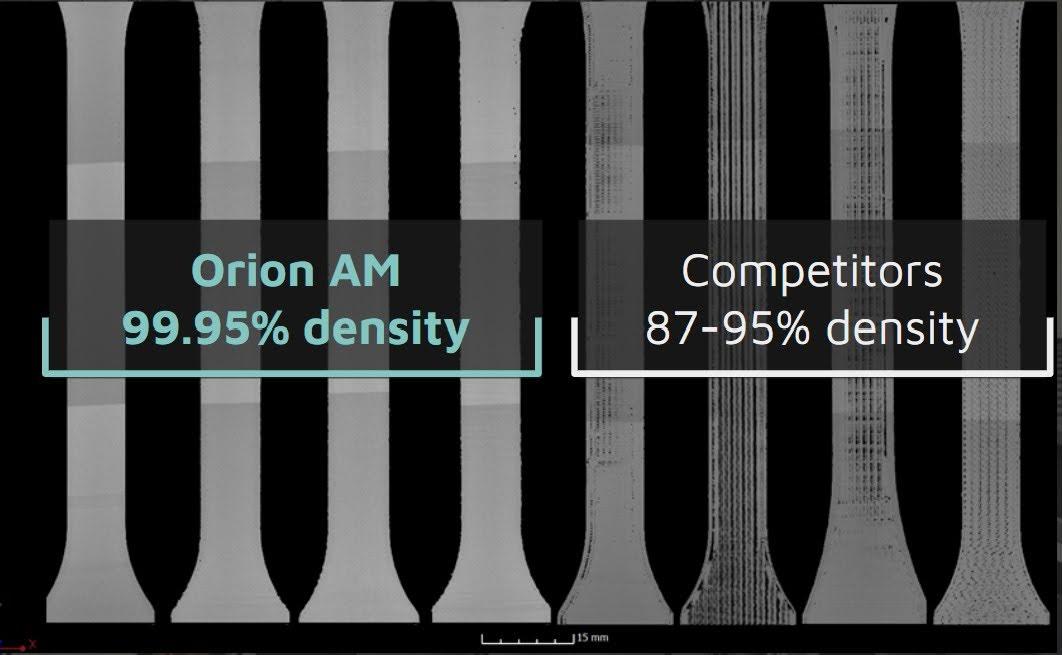
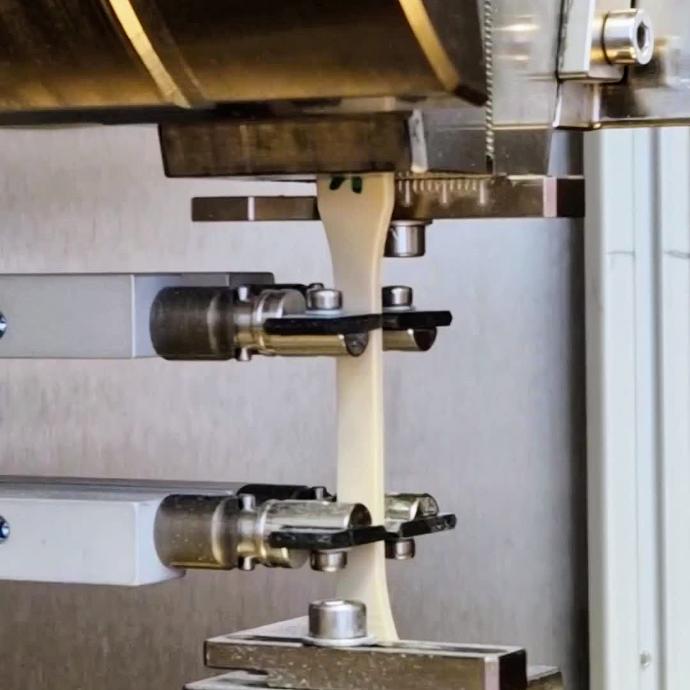
Unrivaled Strength
Orion AM's 3D printing process has been validated with various PEEK material suppliers. The tensile strength results speak for themselves.
Industrial Grade PEEK Filaments
KetaSpire®
PEEK
Tensile Strength (MPa)
Injection Molding Strength: 91 MPa
INFINAM®
9359F
Tensile Strength (MPa)
Injection Molding Strength: 90 MPa

Victrex
AM™450FIL
Tensile Strength (MPa)
Injection Molding Strength: 98 MPa

LUVOCOM® 3F PEEK 9581 NT
Tensile Strength (MPa)
Injection Molding Strength: 95 MPa
KetaSpire®
PEEK CF
Tensile Strength (MPa)
Injection Molding Strength: 159 MPa
Medical/Implantable Grade PEEK Filaments
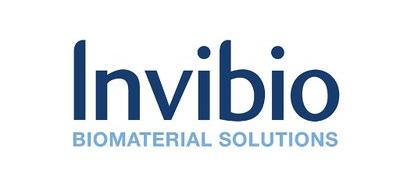
Invibio PEEK-OPTIMA® LT1
Tensile Strength (MPa)
Injection Molding Strength: 100 MPa
VESTAKEEP® PEEK i4 3DF
Tensile Strength (MPa)
Injection Molding Strength: 94 MPa
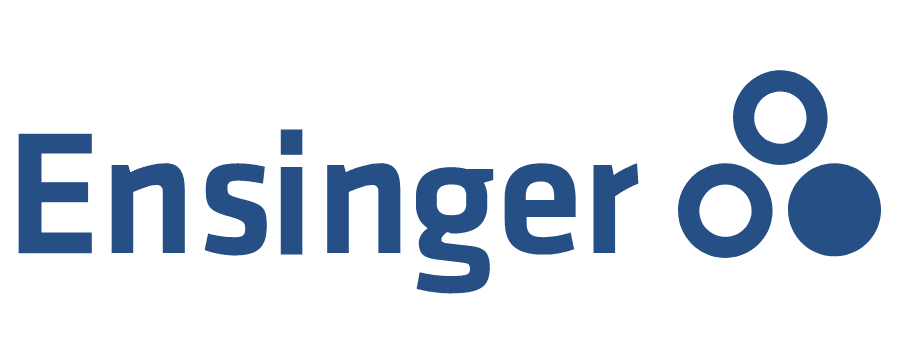
TECAFIL PEEK VX MT
Tensile Strength (MPa)
Injection Molding Strength: 100 MPa
Other High Performance Polymers

Victrex
AM™200FIL
Tensile Strength (MPa)
Injection Molding Strength: 90 MPa
Radel®
PPSU
Tensile Strength (MPa)
Injection Molding Strength: 74 MPa