
Figure N°1 - Testing the MonitorFish
Innovating faster
The idea for the NIMAS project started when the founders of MonitorFish had trouble finding a dependable partner to manufacture their prototype camera housing while keeping up with customer demands. The early prototypes required many design iterations and took a minimum of 4 weeks to manufacture using traditional machining fabrication methods.
The team quickly turned to FFF 3D printing but quickly realized that the resulting parts suffered from delamination and were not watertight. This is when they were introduced to Orion AM, who was working on a revolutionary additive manufacturing process that improves inter-layer bonding, thus the potential to create watertight parts.
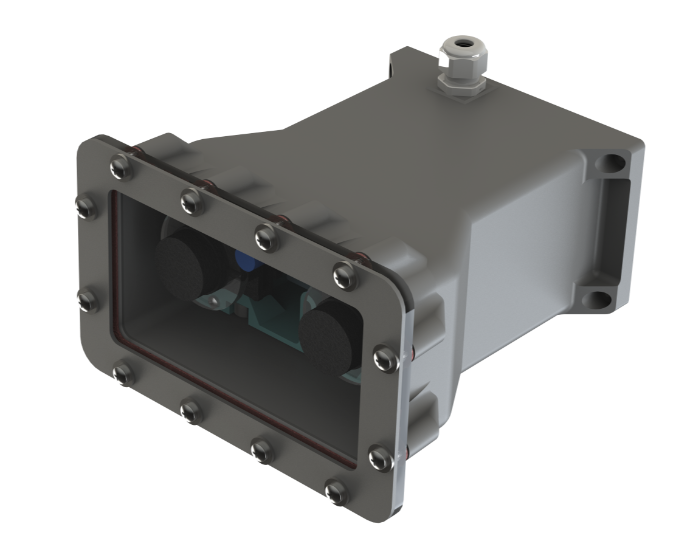
Figure N°2 - 3D Model MonitorFish
Design to Manufacture
The NIMAS camera housing was developed by Orion AM in collaboration with MonitorFish and 3D printed on Orion’s A150 system using ABS material. The design evolved through several iterations, each iteration achieving drastic improvements in functionality, manufacturability, and print time.
The final design took 30 hours to 3D print and required some light post-processing such as sanding and tapping of the threads at the sealing interfaces. After the post-processing, the housing was tested for airtightness at 600mbar vacuum pressure for 48 hours. No chemical processing was required for achieving airtight properties.
The 3D printed solution enables faster innovation by going straight from design to manufacturing of a functional end-use part using Orion AM’s FFF process with a common industrial material. This resulted in a reduction of lead time from 4+ weeks to 48 hours (93% reduction in lead time) and a reduction of costs by approximately 50%.
The laboratory tests revealed impressive mechanical properties, proving that Orion AM’s proprietary Thermal Radiation Heating process not only improves inter-layer bonding but also increases tensile strength, elastic modulus and greatly reduces porosity.
Mechanical Properties | MPa |
Ultimate Tensile Strength -XY | 36.3 |
Ultimate Tensile Strength -XZ | 30.8 |
Ultimate Tensile Strength -ZX | 31.1 |
E-Modulus - XY | 2039 |
E-Modulus - XZ | 1868 |
E-Modulus - ZX | 2096 |
Table N°1 - Mechanical Properties
This project was made possible through the support of the AMable consortium and the help of Phanindra Giddaluri at MonitorFish. A big thanks goes out to Rob Kleijnen at Inspire for his guidance and mentorship, Alice Wise at MTC for her assistance with the design optimizations, and Guy Bex at TNO for the mechanical and porosity testing.