Abstract
At the annual 5th European Space Agency CubeSat Industry Day, Orion Additive Manufacturing GmbH presented its ground-breaking technology for the use of high-performance polymers in 3D printing. Because of Orion’s original Thermal Radiation Heating system, the properties of their 3D printed materials have shown drastic improvements compared to ones printed by other technologies. Recent test results have shown that parts printed with Orion’s technology reached up to 80% of injection-moulded PEEK parts’ theoretical strength. This article explores Orion's research that was presented at ESA's CubeSat Industry Day. Orion is demonstrating how cutting edge additive manufacturing technologies and materials can be used to vastly reduce CubeSat launch costs.
Challenges faced during the production of CubeSats
Challenges faced during the production of CubeSats
Opportunities to improve using Additive Manufacturing
Because each production method requires its own approach to part design, it is often difficult to simply print CubeSat parts that have been designed for traditional manufacture. However, using additive manufacturing does offer some unique freedoms. Especially using FFF, parts can be much more complex, and can be hollowed out. Often, existing parts can also be combined into one, reducing complexity and simplifying assembly. A nice example of this is the ‘kill switch’ found in CubeSats, which ensures the device is not functional until it has been launched. Currently, this is a complex assembly of multiple aluminum frame components, a switch, spring, and plunger. Using the design freedom allowed by the FFF process, this can be reduced to a standard switch with a roller, mounted to a single frame part.![]() | ![]() |
Multiple frame components are needed | The switch, spring, and plunger assembly |
The new design, with a switch integrated into a single printed part |
A 3D Printer for Space
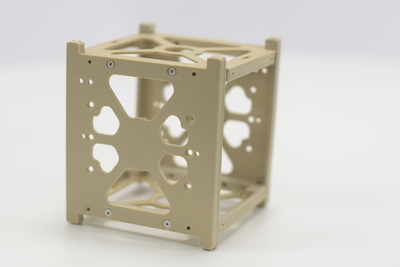
Conclusion
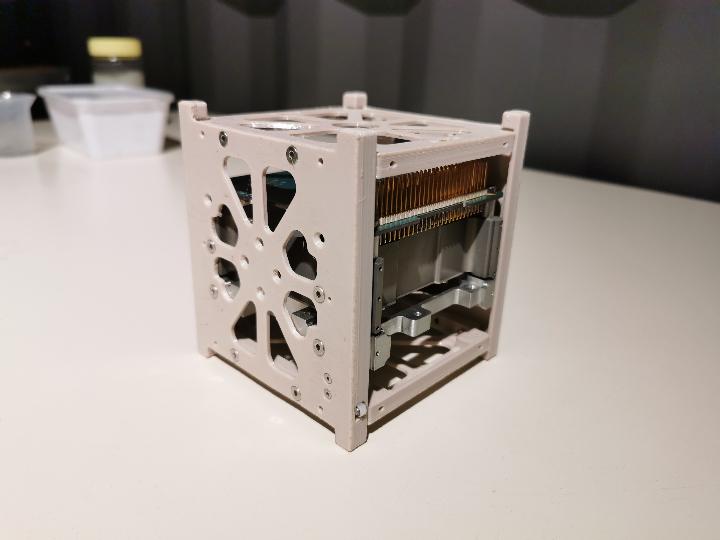